Josh_Br
Rock Crawler
Hello,
I've had an AX-10 for a month or so now. I've done a lot of modifications during that time and I'd like to run through them on here. I started another build thread, but I think it ended up being way too much of me talking and not enough pictures. Personally, I like to see pictures in this sort of thing, and they can tell a lot, without a lot of words. So without any additional chatter from myself, here's what I've done to my rig so far:
Steering:
I spent tons of time messing with the steering setup, trying to get more steering than stock. I'm happy with the results:
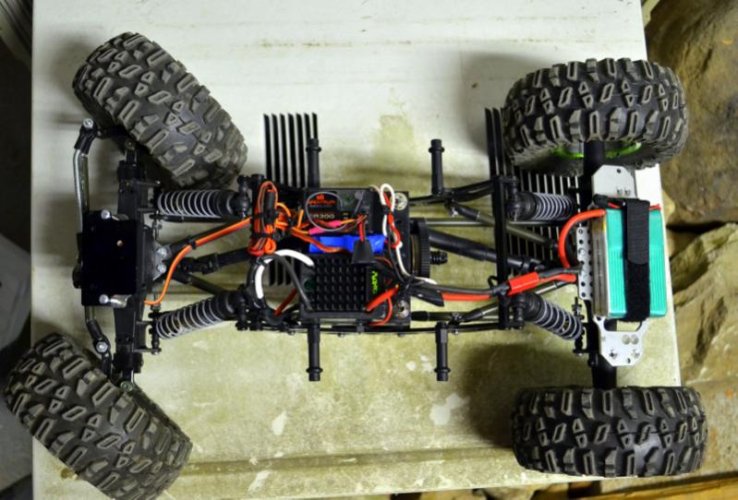
And here is a photo that tells more of the setup:
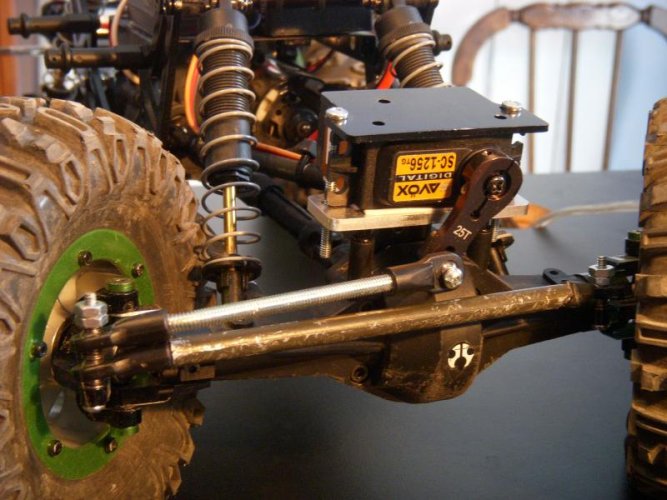
There was a lot that went into getting this increased steering. I'm a little surprised at how involved it was, but I'm really pleased with the results. Here is what it took to go from stock steering to the amount of steering shown in the first photo:
-A high torque servo with greater travel (Savox SC-1256TG).
-A Tx/Rx that has steering travel and end point adjustments (Spektrum DX3C). I wanted the third channel in case I do a front dig some time.
-A longer (and aluminum) servo horn.
-Home made tie rod and drag link. The tie rod gives a little toe-out.
-CVD's
-New c-hubs that use set screws, so the screw heads don't stick out and limit the travel of the knucle arms. They also have added caster.
-Mounting the servo, I had to raise it up about 3/16" with spacers, and set it back a little on the servo plate.
-CC BEC
-Inboarded lower suspension links and moved the shocks in too.
Amazing how one things leads to another and leads to another and......a lesson I should've learned by now! :mrgreen:
I've had an AX-10 for a month or so now. I've done a lot of modifications during that time and I'd like to run through them on here. I started another build thread, but I think it ended up being way too much of me talking and not enough pictures. Personally, I like to see pictures in this sort of thing, and they can tell a lot, without a lot of words. So without any additional chatter from myself, here's what I've done to my rig so far:
Steering:
I spent tons of time messing with the steering setup, trying to get more steering than stock. I'm happy with the results:
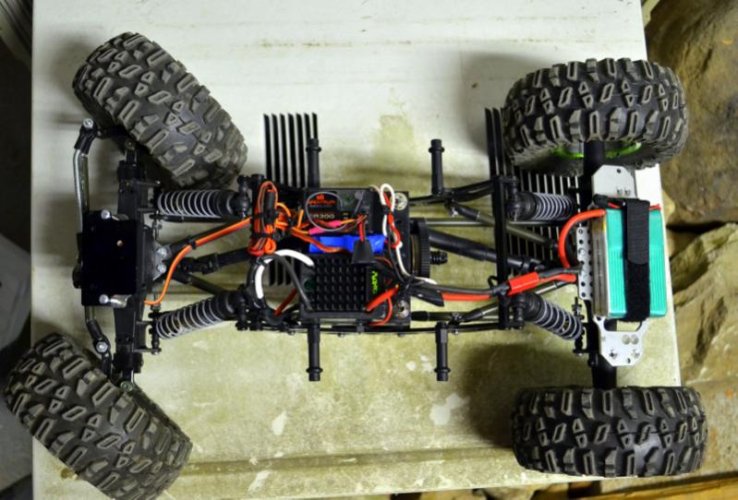
And here is a photo that tells more of the setup:
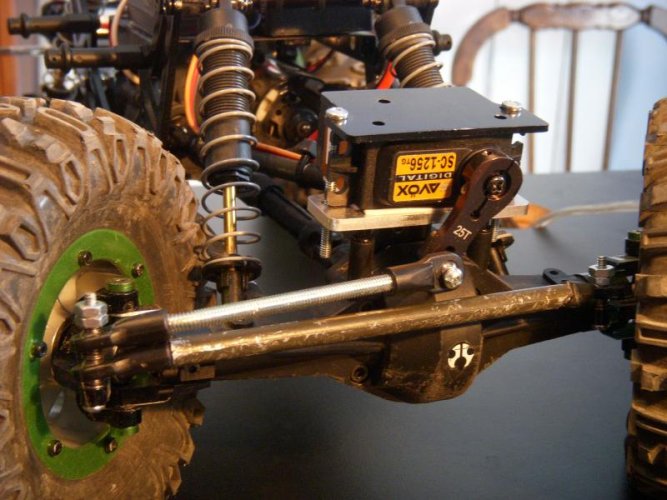
There was a lot that went into getting this increased steering. I'm a little surprised at how involved it was, but I'm really pleased with the results. Here is what it took to go from stock steering to the amount of steering shown in the first photo:
-A high torque servo with greater travel (Savox SC-1256TG).
-A Tx/Rx that has steering travel and end point adjustments (Spektrum DX3C). I wanted the third channel in case I do a front dig some time.
-A longer (and aluminum) servo horn.
-Home made tie rod and drag link. The tie rod gives a little toe-out.
-CVD's
-New c-hubs that use set screws, so the screw heads don't stick out and limit the travel of the knucle arms. They also have added caster.
-Mounting the servo, I had to raise it up about 3/16" with spacers, and set it back a little on the servo plate.
-CC BEC
-Inboarded lower suspension links and moved the shocks in too.
Amazing how one things leads to another and leads to another and......a lesson I should've learned by now! :mrgreen:
Last edited: